Hydraulic Roll Marking Machine: Model 410
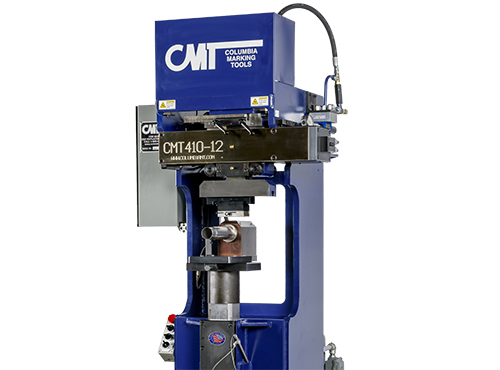
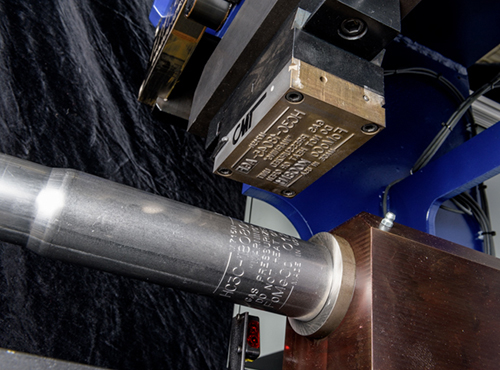
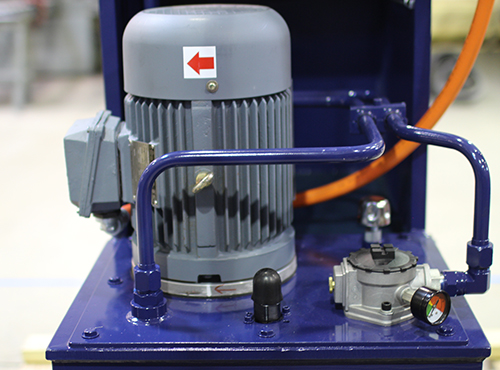
Hydraulic Powered Roll Marking
Floor style industrial weldment to withstand high pressure operation and provide durability.
Hydraulic roll marking machines offer 9 to 18 tons of force and longer stroke lengths, making them ideal for demanding applications. The 410 machine can function as a standalone unit or be seamlessly integrated into a larger production system.
Hydraulic Powered Roll Marking Machines
Ready to run in Industrial High Production
Station Components
The 410 Roll Marking Machine is composed of the following key components:
- Hydraulic-Powered Keyed Ram
- Provides the driving force for marking operations.
- Slide Cylinder
- Provides the secondary driving force for marking operations.
- Controls
- Includes operator interfaces for starting and managing the marking cycle.
- Stamp Holder and Stamps
- Designed to securely hold and position the marking stamps. Upgrades include numbering heads for serial numbering.
- Fixtures and Roll Cradles
- Design to hold or roll part during marking process.
- Frame Options
- Floor style industrial weldment to withstand high pressure operation and provide durability.
- Safety
- OSHA required palm buttons or guarding with a part present cycle start.
Additionally, numbering heads can be mounted on the roll marking machine for specialized numbering applications. A system of air valve devices precisely controls the impact to ensure consistent and accurate marking results.
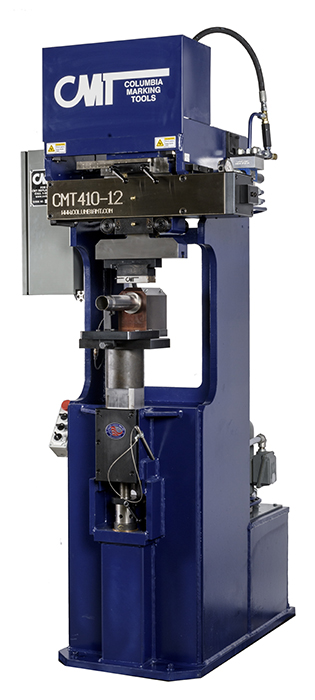
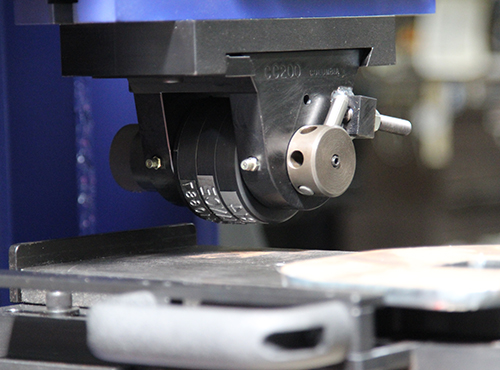
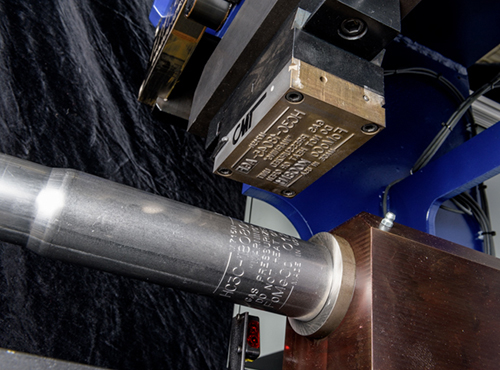
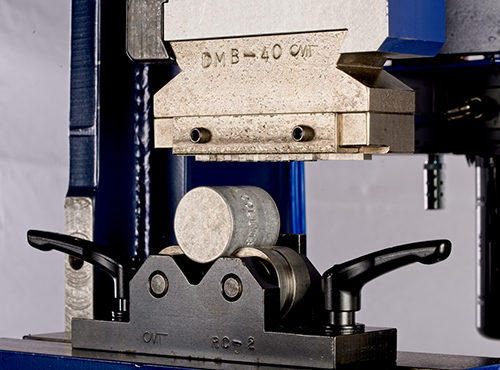
Marking Tooling
Roll marking requires two distinct sets of tooling depending on whether the part being marked is flat or round. Each type of part requires specific dies, holders, and fixturing to ensure precise and consistent marking.
Marking Round Parts
When marking cylindrical or round parts, a flat die or flat holder is used. To ensure a clean and even impression, the part must rotate as it is marked. This is achieved using a roll cradle, which allows the part to roll smoothly under pressure while the die presses the mark into the surface. The rolling motion helps prevent distortion and ensures uniform depth and clarity in the marking.
Marking Flat Parts
Flat parts require a different setup. Instead of a flat die, a round die or roll-type holder is necessary. The round die rotates as it applies pressure to the stationary flat part, imprinting the desired mark. To keep the part stable during the marking process, a part fixture is used to secure it in place, ensuring accuracy and preventing movement that could result in misalignment or inconsistent depth.
Station Details
- Hydraulic powered ram
- Slide Cylinder
- Machine mounted control panel
- Hydraulic cotnrol valves
- Holder (or numbering head) and mandrel support for hollow round part or part fixture.
- Roll cradle for round parts or part holding fixture
- Emergency Stop
- Machine base
The 410-machine shown here is specifically designed for integration into a robotic automated production cell. The palm buttons for manual operation have been removed and replaced with a fieldbus interface, enabling seamless communication with the line PLC.
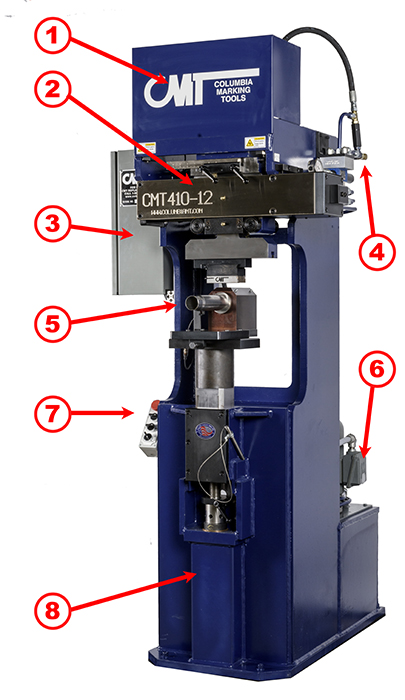